一体化压铸产业链近期得到了市场的广泛关注,很多投资人好奇一体化压铸到底是什么,为什么具备高成长属性,以及我们应该如何理解产业趋势。我们的观点是:一体化压铸技术具备提升生产效率、降低整车重量、节约生产成本等显著优势,是车身制造工艺又一重大技术进步。伴随特斯拉、多家新势力及传统主机厂逐步应用,已进入0到1 的产业验证拐点阶段,有望充分受益车身集成化加速带来产业景气高增,设备端、材料端、模具端、制造端各产业环节均有望受益。本文就让我们来聊聊“一体化压铸从何而来”、“一体化压铸为何成为产业确定趋势”、“一体化压铸核心技术基础”及“远期如何展望产业趋势”,由浅入深剖析下产业趋势下的赛道投资机会,祝您阅读愉快!
1. 一体化压铸是突破设备、材料限制升级而来的铝合金压铸工艺
铝合金已在汽车部件中得到广泛应用,主要的加工工艺分为铸造和形变(锻造、冲压、轧制),铝铸件在汽车用铝占比最高,在汽车用铝中占比约70+%,工艺的主要区别在于铸造铝合金一般用于结构更加复杂部件,而形变铝合金则适用于结构较为简单、对机械性能要求更高的汽车部位。
图表1:按部件系统组划分汽车用铝量
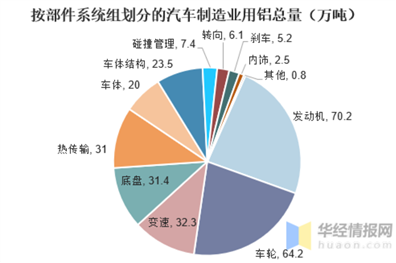
资料来源:华经情报网
图表2:铸造铝合金工艺的分类
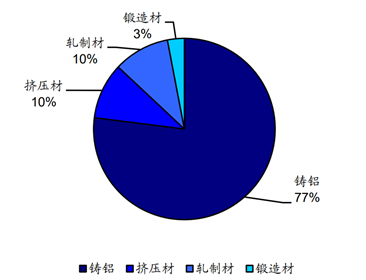
资料来源:海通国际
其中,铸造工艺内部分为压力铸造(高压铸造、真空压力铸造、低压铸造)、重力铸造和挤压铸造三种;其中压铸是汽车常用的铸造方式之一,原理是用压机将金属液压射到模具中。优点是可以生产形状复杂且壁薄的金属零件,压铸材料绝大部分是铝和镁。
图表3:铝合金成型技术对比
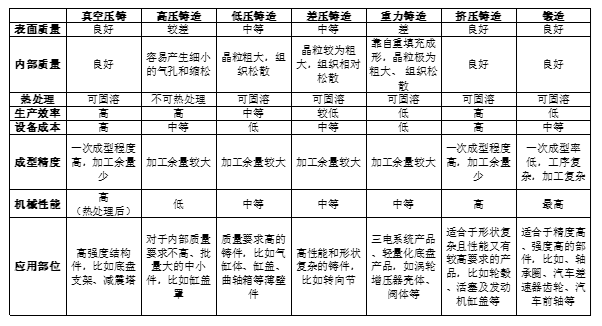
资料来源:银叶投资权益投资部梳理
压铸特别适合制造大量的中小型铸件,同其他技术相比,压铸的表面更为平整,拥有更高的尺寸一致性,适合汽车零件生产且应用广的是压力铸造工艺。但传统高压铸造的缺点产品容易形成气孔缺陷,导致铸件的力学性能变差,限制了压铸件作为构造用部件的适用范围。为了克服传统压铸方法的缺陷,真空铸造和挤压铸造等工艺应运而生。过往压铸工艺在汽车中应用领域广泛,但主要以小型零部件为主。制约压铸材料大型化的发展主要是两个技术难点:压铸机锁模力吨位要求更高+高延伸率的免热处理铝合金。2020年9月,特斯拉为解决产能瓶颈,宣布其Model Y将采用一体化压铸后底板总成,将多个零部件重新设计一次压铸成型,并实现厂内直接供货,缓解因产能不足导致的延迟交付。
2. 一体化压铸是汽车行业降本增效的有效路径
传统车身制造工序先通过冲压、挤压、铸造完成各零部件生产,再使用焊接、铆接工艺将零部件进行连接。传统白车身由300-500个零部件构成,焊接点位可达4000-6000个。由于零部件众多会导致尺寸误差,因此汽车总装出厂前需要进行近6个月总计三轮匹配调试。而一体化压铸则可以通过将多个零件合并为一个,简化生产流程,并将调试时间缩减为1-2轮,有效降低产线的资本投入以及提升生产效率。
图表5:一体化工艺对汽车制造流程的革新
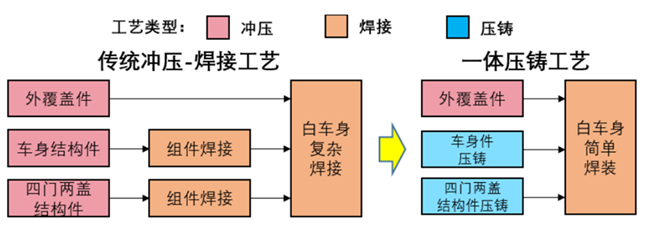
资料来源:中信证券
图表6:传统生产工艺&一体化压铸工艺对比(后底板为例)
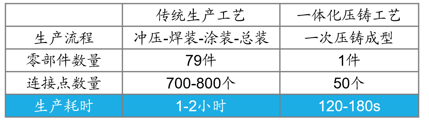
资料来源:银叶投资权益投资部梳理
整体看,一体化压铸的优势可以总结为:1)减少产线投资;2)生产效率提升;3)减少人工成本;4)降低整车重量;5)提高材料利用率;劣势为:1)压铸机、模具成本高;2)后续维修成本高。正如马斯克所说“德州工厂可以实现年产50万辆Model Y完全得益于一体压铸”,特斯拉当前看好一体化压铸路线主要还是为解决产能不足的掣肘,对于成本端的规模优势更多还需量产规模的持续增长来拉动。而市场比较担心的是维修成本高昂的问题,整体来看下车身总成受损概率较小,且一般受损事故都属于整车报废级别的,但我们认为随着一体化压铸的大规模应用,维修成本问题将进一步得到市场的关注与重视。
3. 高吨位压铸机+高精度模具+免热合金材料构成一体化压铸3大硬性基础
设备端:大型一体化成型件需要采用高吨位压铸机,前期由于市场上并无适配超大型一体化压铸件的超大型压铸机,因此一体化压铸也无法实现。2019年特斯拉提出了一种车架一体铸造技术和相关的铸造机器设计,并采用力劲科技子公司意德拉为其定制支持6000吨压铸设备。2021年力劲9000吨超级压铸单元在宁波全球首发,同时近两年国内压铸设备厂商海天集团(8800吨)、伊之密(7000吨)等也相继研发出高吨位大型压铸机。
模具端:大型压铸产品结构复杂,对模具的要求亦进一步增加。1)一体化压铸模具的结构和工序都更加复杂,2)对模仁表面质量要求更高,3)对模具的精度要求不断提高。当前相关模具厂正加快一体化压铸车身结构件模具的研发,部分企业选择与零部件厂商以及主机合作研制,模具环节产品逐渐定制化;除少部分企业具备自研模具能力,多数零部件厂商的模具均需外购。材料端:传统压铸工艺中,需要使用到热处理等工序来提高零部件的机械性能、耐腐蚀性能等。但加热冷却过程中产生的热胀冷缩效应,带来零部件的形变误差,特别是对于一体化的大体积部件,进一步放大了变形风险,因此需采用免热处理铝合金材料来满足产成品不变形和必要的力学性能。目前,国内外均有企业开发和推广免热处理铝合金材料,其中包括了立中集团、帅翼驰、华人运通与上海交大、广东鸿图、特斯拉、美国美铝、德国莱茵菲尔德等,材料性能有一定的差异,并且还有很大的研发提升空间。
图表7:铝合金成型技术对比
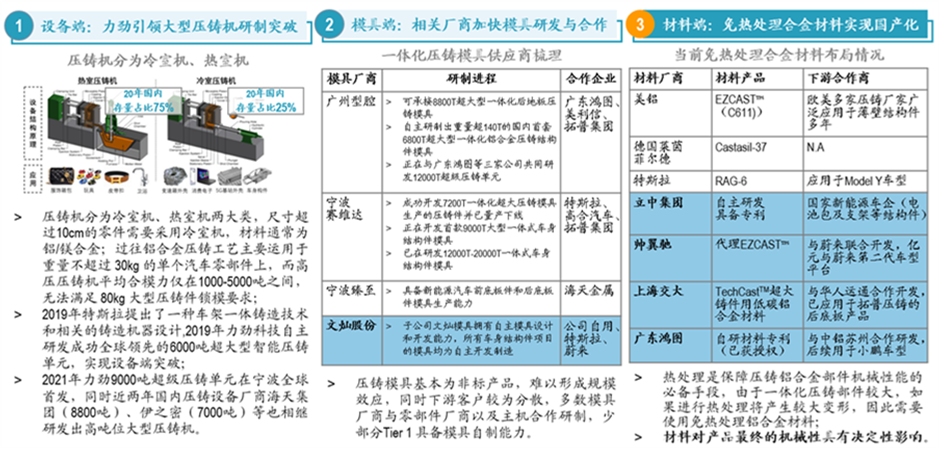
资料来源:银叶投资权益投资部梳理
4. 特斯拉引领成为行业确定趋势,其他主机厂/压铸厂纷纷跟进布局
特斯拉率先推进车身一体化压铸,目前已掌握一体化压铸技术(材料+工艺+外采大型压铸设备),实现Model Y后底板减重30%;但受限于压铸机吨位,下车身一次压铸成型暂分为前/中/后三个部位对370个零部件替换,届时下车身总成质量将进一步下降10%。继特斯拉之后,蔚小理等新势力以及沃尔沃、大众等传统车企均已开始跟进布局和规划应用一体化压铸技术,而国内铝压铸企业也均在加快对大型压铸设备的布局。考虑到新技术导入车型所需的开发周期,预计2024-2025年一体化压铸的市场将迎来显著扩容。
图表8:特斯拉一体化压铸技术储备
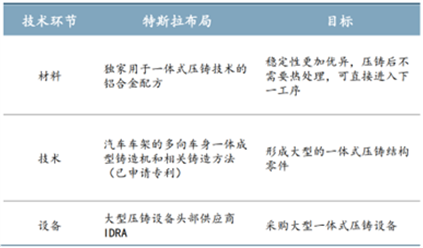
资料来源:中信建投证券
图表9:特斯拉产能及压铸设备分布情况
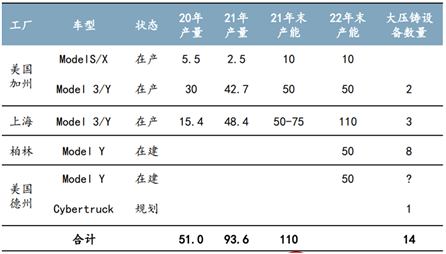
资料来源:中信建投证券
5. 一体化压铸应用场景持续拓宽,行业中长期空间广阔
当前时点看,一体压铸在节约成本、提升效率上的优势已被下游广泛认知,各家实际试样效果也较为理想,后续渗透率有望加速提升。从应用场景看,一体压铸在车身后底板依旧会优先使用,前底板、中部底板以及电池盒托盘的应用则有望逐步拓展。
图表10:当前一体压铸工艺加速渗透四大部位
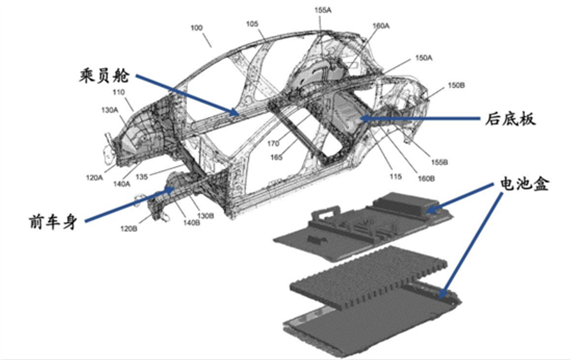
资料来源:海通国际
短期看,后底板已有多个主机厂、零部件厂商试制成功及逐步量产,渗透率有望率先提升。而随着压铸设备吨位和压铸工艺进一步提升,一体化压铸相对于挤出+焊接路线的成本优势将得到凸显,中底板与电池托盘渗透率也有望实现加速提升。但考虑到碰撞风险及后续维修难度,我们认为一体化压铸将主要被应用于后底板、中底板和电池盒托盘部位。正如前文所述,特斯拉之所以坚定地选择一体化压铸路线主要是为了缓解因产能不足导致的延迟交付。而根据我们测算,当一体化压铸产线的产能利用率低于80%时,就很难实现经济效益,成本优势将被大幅削弱。当前每条一体化压铸产线对应年产能约10万件,因此,我们认为一体化工艺将在月销过万的中高端新能源车型中加速渗透。
风险提示:本文涉及的相关信息仅供参考,不构成产品要约,不构成证券的投资建议。
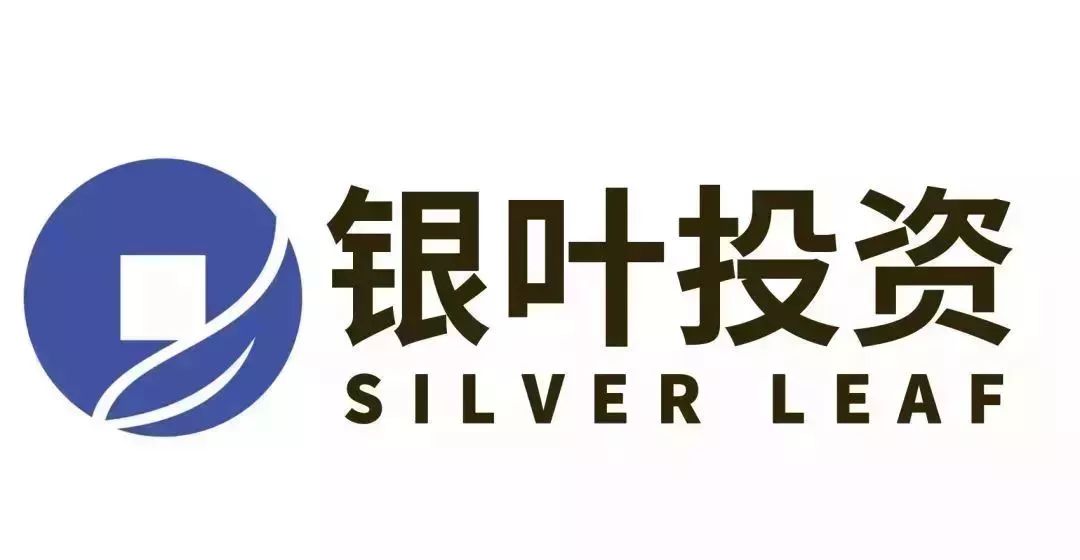
上海银叶投资有限公司成立于2009年2月,是一家综合型专业资产管理机构。公司是中国证券投资基金业协会(AMAC)普通会员、中国银行间市场交易商协会会员、人民币利率互换市场和远期利率市场成员。依靠长期深耕中国资本市场积累的专业优势,银叶投资已经形成覆盖固定收益、宏观对冲、权益投资、量化及衍生品策略等多元化的投资体系。公司愿景是成为顶尖的基金管理人,秉承专业、诚信、责任、创新的企业理念,为机构投资者和高净值客户提供多策略资产配置方案,实现绝对收益基础上的长期稳定回报,创造价值,分享价值,为资产管理事业贡献力量。
上海银叶投资有限公司
微信号:yytz_am
电话:021-61080888
地址:浦东新区花园石桥路66号东亚银行金融大厦
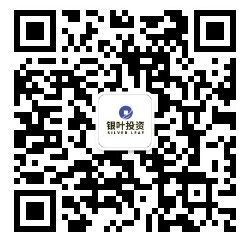